@Disla , I also simulated by defining the amplitude for each element and it worked as given below.
*Cflux, Amplitude=Node1, Add
N1, 11, 100000
…
*Amplitude, Name=Tabular-1, Time=Total time
0, 0, 5, 0, 25, 1, 30, 1,
35, 0, 75, 0, 80, 1, 85, 1,
90, 0, 100, 0
*Amplitude, Name=Node1
0, 0, 5, 1, 10, 1, 15, 0,
500, 0
*Amplitude, Name=Node2
0, 0, 15, 0, 20, 1, 25, 1,
30, 0, 500, 0
…
Here, I did not use dflux.f.
But, my interest is to use dlux.f and avoid individual element or node definitions. If I am not wrong, we can do the moving heat source using the dflux file as referred by @Calc_em . Here we can avoid individual element definitions.
@Calc_em, can you please post an inp file and corresponding dflux file for my reference? alternatively, If you give me your mail ID, I will send my deck files
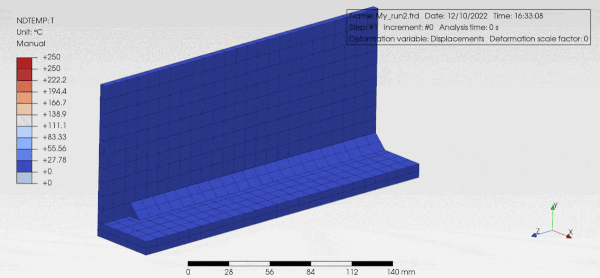
for your verification.